Fig. 1 — U.S. Navy F/A 18F Super Hornet completes its first carrier night operations. Low-pressure vacuum carburizing is applied to aircraft parts such as braking systems, actuator systems, flight controls and guidance systems, hydraulic power plants, and landing gearboxes. Image courtesy Boeing.
Low-Pressure Vacuum Carburizing
Daniel H. Herring*
The Herring Group Inc. Elmhurst, Illinois Frederick J. Otto*
Midwest Thermal-Vac Kenosha, Wisconsin
Low-pressure vacuum carburizing, a technology developed in the mid 1990’s, has helped revolutionize the heat treating industry, primarily because of its capability for precise process control. Tight control enables absolute repeatability, optimized part microstructure, enhanced mechanical properties, and reduced manufacturing costs.
Demand for vacuum carburizing systems equipped with high pressure gas quenching, direct oil quenching, or both has quadrupled since 2000, as the technology has replaced atmosphere carburizing and traditional oil quenching in many cases. New materials (Table) designed specifically for high-temperature service retain their hardness and mechanical properties well into a service range of 600 to 950ºF (315 to 510ºC) and higher. Many are similar in chemistry to stainless and tool steels to take advantage of higher resistance to corrosion and wear, but they have better core microstructures.
Vacuum carburizing technology Temperature uniformity is critical for vacuum carburizing, especially in the low-temperature ranges, and
a maximum spread of ±10ºF (±5.5°C) is required to maintain tight case depth control throughout the load. This is equally important for vacuum carbonitriding cycles, which are run as low as 1425ºF (775ºC). Highly loaded gears and shafts, such as those in off-road vehicles under extreme race conditions, require fracture toughness values two or three times those of conventional vehicles. Tightly controlled low-pressure vacuum carburizing processes deliver these high-performance values.
Case depth control: Effective case depth ranges for vacuum-carburized parts routinely vary from 0.010 to0.250 in. (0.25 to 6.35 mm). Maximum case variation within a load can be held to within 0.005 in. (0.125 mm), and this is routine for aerospace and motorsports components. In one particular vacuum carbonitriding application, the specification called out an extremely shallow case, 0.0005 to 0.0025 in., and the final part variation achieved was 0.0018 to 0.0022 in.
Advanced carburizing alloys
Material |
Carbon, % |
Significant alloying additions, % |
|
Material |
Carbon, % |
Significant alloying additions, % |
---|
XD15NW |
0.37 |
Cr (15.5), Mo, V, Ni |
|
CSS-42L |
0.12 |
Cr (14.0), Co, Mo, Ni, V, Cb |
X13VDW |
0.12 |
Cr (11.5), Ni, No, V |
|
CSB-50NIL |
0.13 |
Mo (4.25), Cr, Ni, V |
AF1410 |
0.15 |
Co (14.0), Ni, Cr, Mo |
|
Pyrowear 675 |
0.07 |
Cr (13.0). Ni, Mo, V |
CBS 223 |
0.15 |
Cr (4.95), Co, Mo |
|
Pyrowear 53 |
0.10 |
Mo (3.25), Ni, Cr, Si |
CBS-600 |
0.19 |
Cr (1.45) Mo, Si |
|
AerMet 100 |
0.23 |
Co(13.4), Ni, Cr, Mo |
BG42 |
1.15 |
Cr (14.5) Mo, V |
|
HP 9-4-30 |
0.30 |
Ni (9.0), Co, Cr |
N360 Iso Extra |
0.33 |
Cr (15.0), Mo, Ni |
|
HY-180 |
0.13 |
Ni (10.0), Cr. Mo |
N695 |
1.05 |
Cr (17.0), Mo, Si |
|
R250 |
0.83 |
Mo (4.30), Cr, V |
EN30B |
0.32 |
Cr (1.30), Mo, Si |
|
R350 |
0.14 |
Mo (4.30), Cr, Ni |
Cronidur 30 |
0.31 |
Cr (17.0), Mo, Si, Ni |
|
C61 |
0.16 |
Co (18.0), Ni, Cr, Mo |
CS62 |
0.08 |
Co (15.0), Ni, Cr, V |
|
VascoMax C-250 |
0.03 max |
Ni (18.5), Co, Ni, Cb |
C69 |
0.10 |
Co (28.0), Cr, Ni, Mo, V |
|
VascoMax C-350 |
0.03 max |
Ni (18.5), Co, Ni, Cb |
Surface carbon: Surface carbon is controlled in the range of 0.60 to 0.80% for most conventional materials, and between 0.45 and 0.75% for many advanced materials. Controlling retained austenite levels is also important.
Hardness: The new materials require better control of hardness and carbon distribution (case/core hardness, surface/near surface), optimized microstructures, and control of such factors as retained austenite, carbide size (type and distribution), and non-martensitic phases. Property control is also critical, especially for characteristics such as residual stress patterns and surface finish, and mechanical properties such as toughness, impact strength, and wear resistance.
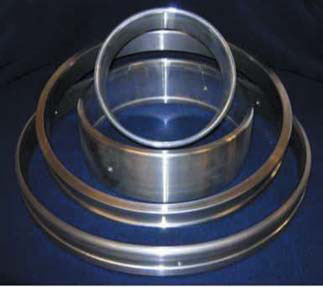 Improving performance. Improved performance demands in aircraft and rotorcraft not only are pushing the development of advanced materials, but also are driving prime contractors and their suppliers to low-pressure vacuum carburizing.
Typical commercial and military aircraft applications of low-pressure vacuum carburizing include braking systems, actuator systems, flight controls and guidance systems, hydraulic power plants, landing gearboxes, and components such as bearings, ball screws and nuts, planetary gears, pinions, and shafts.
Specification updates
Aerospace and automotive specifications need to be reviewed in light of the rapid developments underway with these new materials. Serious consideration must be given to carburizing such materials above conventional carburizing temeperatures, to minimize cycle times and reduce carbon absorption.
Extensive work is underway to optimize part microstructure at these elevated temperatures. Pre-oxidation treatments have been found to be unnecessary, and rules for the application of high gas pressure quenching need to be better established. Once these goals are achieved, low-pressure vacuum carburizing technology offers almost unlimited possibilities.
To improve part performance throughout the industry, commercial heat treaters are beginning to share their knowledge with respect to successes and lessons learned.
Part cleanliness has improved because of the development of aqueous, semi-aqueous, and solvent-based cleaning technology.
Elimination of manufacturing steps such as pre-oxidation is helping to improve quality.
Lead times are being reduced and process control improvements are better documented.
Preventive maintenance practices result in up-time reliability greater than 95%.
Better process specifications and detailed guidelines for high-pressure gas quenching are being actively pursued throughout the industry.
For more information: Dan Herring, the Herring Group Inc., P.O. Box 884, Elmhurst, IL 60126-0884; tel: 630/834-3017; fax: 630/834-3117; dherring@heat-treatdoctor.com; www.heat-treat-doctor.com. Fred Otto, Midwest Thermal-Vac, 5727 95th Avenue, Kenosha, WI 53144; tel: 262/605-4848; fredotto@mtvac.com; www.mtvac.com.
ADVANCED MATERIALS & PROCESSES/MARCH 2007
For more information visit our Resources page.
Vacuum Carburizing |
Heat Treat |Plasma
Nitriding | Vacuum
tempering | Directory | Resources
All mtvac.com content is copyright© MtVac2020
|