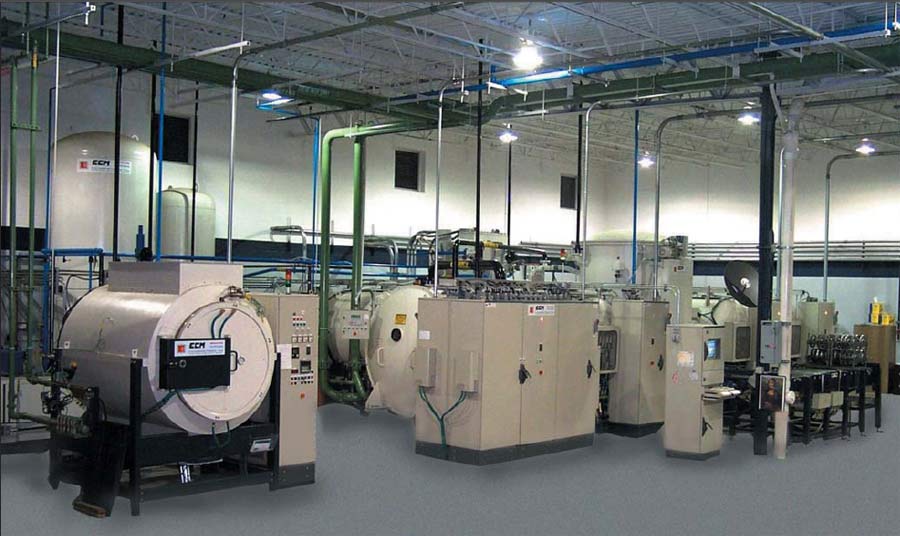
OF NEW AEROSPACE AND MOTORSPORTS MATERIALS
Demand for vacuum
carburizing systems
equipped with high
pressure gas quenching,
oil quenching, or both has
quadrupled since 2000.
Commercial heat treating
has seen the second
largest increase in the
number of installed low
pressure vacuum
carburizing units. Frederick J. Otto**
Daniel H. Herring** ** Member of ASM International and member, ASM Heat Treating Society |
Progress continues to be made
in low pressure vacuum carburizing
for advanced applications
in the aerospace and
motorsports markets since 2005 [1],
particularly in the development of
carburizing cycles for new materials
and materials previously not vacuum
carburized. Materials successfully
vacuum carburized reported in 2005
included: • Aubert & Duval X12 VDW and XD15NW • Carpenter Technology Corp. Pyrowear 53 and 675 • Böhler-Uddeholm N360 Iso Extra, N695, R250, R350 • Questek Innovations Ferrium C61, CS62, C69, M60S, and S53 • Timken Company CSS-42L, CSB- 50NIL, CBS-600, and BG42VIM/ VAR • Atlas Specialty Steels BS970 EN30B New grades carburized since that time include: • CarTech AerMet 100 • Timken CBS 223, AF1410, HY180, HP-9-430, and 300M • VSG Essen Cronidur 30 • Teledyne Corp. VascoMax C-250, C-300, and C-350 In addition, the range of carburizing case depths for all grades has been extended extensively in the past two years (Table 1). What Has Been Achieved MTV studied critical process parameters and their interactions including: • Required temperature uniformity • Methods of carbide control • Avoidance of carbide networks and necklace formation • Surface carbon control • Achievable case uniformity • Maximum achievable core properties • Quenching parameters for distortion sensitive and distortion prone part geometry Effective case depths have been extended to 0.080-0.120 in. (2 0-3.0 mm), and beyond, without significant sacrifice of microstructure. The range of carburizing temperatures now includes the use of high temperature techniques. |
Table 1 — Production cycle process parameter interaction
Material | Achievable ECD, in. (mm) | Temp. range, °F (°C) | Core hardness, HRC | Case hardness, HRC | Surface carbon, % |
---|---|---|---|---|---|
X13VDW | 0.015-0.100 (0.38-2.55) | 1675-1900 (915-1040) | 43-46 | 59-63 | 0.86-1.05 |
XD15NW | 0.015-0.065 (0.38-1.65) | 1700-1950 (925-1065) | 36-55 | 58-64 | 0.72-0.92 |
Pyrowear 675 | 0.015-0.095 (0.38-2.40) | 1600-1925 (870-1050) | 39-43 | 62-66 | 0.875-1.2 |
Pyrowear 53 | 0.015-0.085 (0.38-2.15) | 1600-1850 (870-1010) | 3640 | 59-63 | 0.55-0.72 |
AerMet 100 | 0.015-0.060 (0.38-1.53) | 1600-1650 (870-900) | 52-55 | 58-63 | 0.57-0.79 |
N360 Iso Extra | 0.015-0.035 (0.38-0.90) | 1675-1925 (915-1050) | 56-58 | 63-67 | 0.60-0.72 |
N695 | 0.025-0.55 (0.65-1.40) | 1650-2020 (900-1105) | 55-60 | 62-65 | 0.56-0.69 |
R250 | 0.020-0.045 (0.50-1.15) | 1680-1825 (915-1000) | 50-52 | 62-64 | 0.65-0.78 |
R350 | 0.025-0.060 (0.65-1.53) | 1680-2010 (915-1100) | 52-55 | 63-66 | 0.66-0.82 |
C61 | 0.015-0.100 (0.38-2.55) | 1900-2025 (1040-1110) | 48-52 | 60-70 | 0.42-0.53 |
CS62 | 0.015-0.045 (0.38-1.15) | 1900-2025 (1040-1110) | 49-51 | 60-62 | 0.40-0.48 |
C69 | 0.015-0.100 (0.38-2.55) | 1850-1925 (1010-1050) | |||
CSS-42L | 0.015-0.075 (0.38-1.90) | 1650-2050 (900-1120) | 28-45 | 58-69 | 0.55 – 0.70 |
CSB-50NIL | 0.015-0.060 (0.38-1.53) | 1650-2050 (900-1120) | 47-50 | 58-63 | 0.62-0.83 |
CBS-600 | 0.015-0.075 (0.38-1.90) | 1525-1750 (830-955) | 40-43 | 58-64 | 0.78-1.00 |
BG42 | 0.015-0.065 | 1650-1850 | 44-47 | 61-64 | <0.65-0.88 |
AF1410 | 0.015-0.075 (0.38-1.90) | 1525-1650 (830-900) | 47-49 | 58-62 | 0.84-1.05 |
HY180 | 0.015-0.075 (0.38-1.90) | 1500-1550 (815-845) | 44-47 | 58-62 | 0.82-1.10 |
HP-9-420 | 0.015-0.045 (0.38-1.15) | 1500-1600 (815-870) | 39-42 | 56-59 | 0.95-1.25 |
HP-9-430 | 0.015-0.075 (0.38-1.90) | 1525-1700 (830-925) | 47-50 | 58-62 | 0.85-1.05 |
300M | 0.015-0.045 (0.38-1.15) | 1600-1700 (870-925) | 53-55 | 58-62 | 0.80-0.92 |
BS 970 EN30B | 0.015-0.055 (0.38-1.40) | 1550-1750 (845-955) | 52-54 | 58-62 | 0.65-0.825 |
VSG Essen Cronidur 30 | 0.020-0.055 (0.50-1.40) | 1600-1890 (870-1030) | 55-57 | 62-66 | 0.58-0.77 |
VascoMax C-250 | 0.015-0.075 (0.38-1.90) | 900-1525 (480-830) | 48-50 | 57-61 | 0.82-0.95 |
VascoMax C-300 | 0.015-0.075 (0.38-1.90) | 900-1525 (480-830) | 51-54 | 58-62 | 0.82-0.97 |
VascoMax C-350 | 0.015-0.075 (0.38-1.90) | 900-1525 (480-830) | 55-59 | 59-62 | 0.83-1.02 |
Progress continues to be made in low pressure vacuum carburizing for advanced aero and motorsports applications. Improved mechanical properties such as fracture toughness and enhanced corrosion resistance have been achieved in many new aero and motorsport materials using precision vacuum carburizing. |
All these materials required
extensive development testing to produce custom designed recipes to optimize cycle parameters. Some of the new techniques developed
to achieve these results within an existing recipe required changes to temperature, flow rate, pressure, and hydrocarbon type. Also, high pressure gas quench-ing methods involved
the use of various gas mixtures
(nitrogen, nitrogen/hydrogen, and carbon dioxide/helium) in addition
to vacuum oil quenching.
Application to Advanced Materials
Control of Microstructure |
Content, wt% | |||||||||||||
---|---|---|---|---|---|---|---|---|---|---|---|---|---|
C | Mn | Cr | Ni | Mo | Si | V | Co | Nb | Ti | Al | Zr | B | |
XD15NW | 0.37 | — | 15.5 | 0.20 | 1.80 | — | 0.30 | — | — | — | — | — | — |
X13VDW | 0.12 | — | 11.5 | 2.50 | 1.60 | — | 0.03 | — | — | — | — | — | — |
Pyrowear 675 | 0.07 | 0.65 | 13.0 | 2.60 | 1.80 | 0.40 | 0.60 | 5.40 | — | — | — | — | — |
Pyrowear 53 | 0.10 | 0.35 | 1.00 | 2.00 | 3.25 | 1.00 | 0.10 | — | — | — | — | — | — |
AerMet 100 | 0.23 | — | 3.10 | 11.10 | 1.20 | — | — | 13.4 | — | — | — | — | — |
N360 Iso Extra | 0.33 | 0.50 | 15.0 | 0.40 | 1.00 | — | — | — | — | — | — | — | — |
N695 | 1.05 | 0.20 | 17.0 | — | 0.50 | 0.50 | — | — | — | — | — | — | — |
R250 | 0.83 | 0.70 | 4.00 | — | 4.30 | 0.20 | 1.10 | — | — | — | — | — | — |
R350 | 0.14 | 0.30 | 4.25 | 3.50 | 4.30 | 0.18 | — | — | — | — | — | — | — |
C61 | 0.16 | — | 3.5 | 9.5 | 1.1 | — | 0.08 | 18.0 | — | — | — | — | — |
CS62 | 0.08 | — | 9.0 | 1.5 | — | — | 0.2 | 15.0 | — | — | — | — | — |
C69 | 0.090.11 | — | 5.0-5.2 | 2.9-3.1 | 2.4-2.6 | — | 0.015-0.025 | 27.8-28.2 | — | — | — | — | — |
CSS-42L | 0.12 | — | 14.0 | 2.00 | 4.75 | — | 0.60 | 12.5 | 0.02 | — | — | — | — |
CSB-50NIL | 0.13 | 0.25 | 4.20 | 3.40 | 4.25 | 0.20 | 1.20 | — | — | — | — | — | — |
AF1410 | 0.13-1.17 | 0.10 | 1.8-2.2 | 9.5-10.5 | 1.0 | 0.10 | — | 13.5-1 4.5 | — | — | — | — | — |
CBS 223 | 0.15 | 0.40 | 4.95 | 0.10 | 1.45 | 0.90 | — | 1.55 | — | — | 0.05 | — | — |
CBS-600 | 0.19 | 0.60 | 1.45 | — | 1.0 | 1.1 | 0.06 | — | — | — | 0.06 | — | — |
BG42 | 1.15 | 0.50 | 14.5 | — | 4.00 | 0.30 | 1.20 | — | — | — | — | — | — |
HP 9-4-30 | 0.29-0.34 | 0.35 | 0.90-1.10 | 8.00-9.50 | — | 0.20 | — | 4.25-4.75 | — | — | — | — | — |
HY-180 | 0.13 | 0.10 | 2.0 | 10.0 | 1.0 | 0.05 | — | — | — | — | — | — | — |
300M | 0.38-0.46 | 0.6-0.9 | 0.7-0.95 | 1.65-2.0 | 0.30-0.65 | 1.45-1.8 | 0.05 min | — | — | — | — | — | — |
835M30 EN30B ANN | 0.26-0.34 | 0.45-0.70 | 1.10-1.40 | — | 0.20-0.35 | 0.10-0.35 | — | — | — | — | — | — | — |
Cronidur 30 | 0.31 | — | 17.0 | 0.38 | 1.02 | <0.55 | — | — | — | — | — | — | — |
VascoMax C-250 | 0.03 max | 0.10 max | — | 18.5 | 4.80 | 0.10 max | — | 7.50 | 0.40 | 0.10 | — | 0.01 | 0.003 |
VascoMax C-300 | 0.03 max | 0.10 max | — | 18.5 | 4.80 | 0.10 max | — | 9.00 | 0.60 | 0.10 | — | 0.01 | 0.003 |
VascoMax C-350 | 0.03 max | 0.10 max | — | 18.5 | 4.80 | 0.10 max | — | 12.00 | 1.40 | 0.10 | — | 0.01 | 0.003 |
Aerospace Industry
Improved performance demands in aircraft and rotorcraft are not only pushing advanced materials, but also are forcing prime contractors and their suppliers to use low pressure vacuum carburizing in more challenging
applications. Typical commercial
and military applications (Fig. 5 and 6) of low pressure vacuum carburizing for aerospace vehicles include such items as braking systems,
actuator systems, flight controls
and guidance systems, hydraulic
power plants, and landing gearboxes, and involves components
such as bearings, ball screws and nuts, planetary gears, pinions, and shafts. The commercial heat treating in-dustry is beginning to share its wealth of knowledge with respect to acknowledged successes and lessons learned. Improved cleaning tech-nology (including rinsing and drying), as well as the elimination of manufacturing steps such as pre-ox-idation, are helping to improve quality. Lead times are being reduced and process control improvements are better documented along with maintenance records and up-time re-liability. What is needed going for-ward are better specifications and rules for the use of high pressure gas quenching.
Table 3 — Achievable performance enhancements
Material | Surface hardness, HRC | UTS, MPa (ksi) | YS 0.2% offset, MPa (ksi) | Charpy V-notch impact energy, N • m• lbf) | Fracture toughness, MPa (ksi) | Tempering temp., °C (°F) |
---|---|---|---|---|---|---|
Carburizing (vacuum) | ||||||
4340 | 53 | 1,979 (287) | 1,862 (270) | 20.3 (15) | 331 (48) | 205 (400) |
4340 | 46 | 1,496 (217) | 1,365 (198) | 29.8 (22) | 489 (68) | 425 (800) |
4340 | 40 | 1,241 (180) | 1,158 (168) | 47.5 (35) | 689 (100) | 540 (1000) |
H11 | 56 | 2,006 (291) | 1,675 (243) | 20.3 (15) | 331 (48) | 540 (1000) |
H11 | 48 | 1,641 (238) | 1,413 (205) | 27.1 (20) | 427 (62) | 580 (1075) |
H11 | 44 | 1,427 (207) | 1,276 (185) | 31.2 (23) | 483 (70) | 595 (1100) |
300M | 56 | 2,344 (340) | 1,241 (180) | 17.5 (13) | 310 (45) | 95 (200) |
300M | 54 | 2,137 (310) | 1,655 (240) | 21.7 (16) | 345 (50) | 205 (400) |
300M | 45 | 1,793 (260) | 1,482 (215) | 13.6 (10) | 235 (34) | 425 (800) |
300M | 40 | 1,586 (230) | 1,358 (197) | 42.0 (31) | 689 (100) | 540 (1000) |
EN30B | 52 | 1.793 (260) | 1489 (216) | 36,6 (27) | 565 (82) | 205 (400) |
EN30B | 40 | 1.400 (203) | 1289 (187) | 44,7 (33) | 689 (100) | 540 (1000) |
Carburizing (vacuum) | 300M | 63/65 | 2,344 (340) | 1,241 (180) | 17.5 (13) | 310 (45) | 95 (200) |
300M | 61/63 | 2,137 (310) | 1,655 (240) | 21.7 (16) | 345 (50) | 205 (400) |
AerMet 100 | 61/63 | 1,931 (280) | 1,724 (250) | 56.9 (42) | 827 (120) | 480 (900) |
AerMet T | 61/63 | 1,965 (285) | 1,724 (250) | 33.9 (25) | 558 (81) | 480 (900) |
AerMet 310 | 61/63 | 2,172 (315) | 1,896 (275) | 27.1 (20) | 448 (65) | 480 (900) |
AF1410 | 59/62 | 1,813 (263) | 1,586 (230) | 80.0 (59) | 1.255 (182) | 495 (925) |
AF1410 | 58/61 | 1,710 (248) | 1,551 (225) | 93.6 (69) | 1.469 (213) | 510 (950) |
EN30B | 62/65 | 1,793 (260) | 1,489 (216) | 36.6 (27) | 565 (82) | 95 (200) |
EN30B | 58/62 | 1,400 (203) | 1,289 (187) | 44.7 (33) | 689 (100) | 205 (400) |
Pyrowear 53 | 59/63 | 2,000 (290) | 1,620 (235) | 38.0 (28) | 517 (75) | 315 (600) |
VascoMax C-250 | 61/63 | 1,792 (260) | 1,758(255) | 50.2 (37) | 786 (114) | 480 (900) |
VascoMax C-300 | 61/63 | 2,027 (294) | 1,999 (290) | 28.0 (28) | 517 (75) | 480 (900) |
VascoMax C- 350 | 61/63 | 2,413 (350) | 2,344 (340) | 13.5 (10) | 234 (34 ) | 480 (900) |
Fig. 1 — (a) AerMet 100 vacuum carburized to 0.055 in. (1.40 mm) ECD: 58 HRC @ 0.045 in. (1.15 mm); 60-62
HRC
surface hardness;
(b) microindentation hardness traverse. 1250X
Fig. 2 — (a) AF1410 vacuum carburized to 0.055 in. (1.40 mm) ECD: 60 HRC @ 0.032 in. (0.82 mm); 60-62 HRC
surface
hardness; (b) mi0.005
croindentation hardness traverse. 1250X
Fig. 3 — (a) CBS-223 vacuum carburized to 0.057 in. (1.45 mm) ECD: 63-65 HRC; (b) microindentation hardness
traverse. 1250X
Fig. 4 — (a) X13 VDW vacuum carburized to 0.035 in. (0.89 mm) ECD: 63-65 HRC; (b) microindentation hardness
traverse. 1250X
![]() ![]()
|
Table 4 — Final 2006 NASCAR/Nextel and Busch Series Racing Results ![]() Motorsports Update MTV’s continued participation in motorsports (racecars, dragsters, off-road vehicles, trucks, and top fuel funny cars) has helped produce im-pressive results (Table 4). Race teams embracing low pressure vacuum car-burizing have grown steadily. Highly loaded gear applications such as those in 3,500 hp top fuel dragsters (Figs. 7 and 8) require crankshaft fracture toughness values 2 or 3 times normal values. When the bottom end fails in one of these races, the engines literally explode. Where the Market is Headed
Reference:
|
Vacuum Carburizing |
Heat Treat |Plasma
Nitriding | Vacuum
tempering | Directory | Resources
All mtvac.com content is copyright© MtVac2020